Surface Treatment
We provide surface treatment to our products to satisfy specific customer needs.
Common Plating
We offer common types of surface treatment including zinc plating, nickel plating, chrome plating, tin plating, silver plating, gold plating, palladium plating, palladium nickel plating and copper plating, etc. We also perform various metal alloy plating that requires a higher level of expertise and experience.
Special Surface Treatment
Spot Plating and Laser Scraping
Partial plating on the surface, called spot plating, is widely used in precious metals such as gold to cut down costs by reducing gold consumption. By coating partial metal layer to finished parts and then scraping off excessive portion by means of laser irradiation, this method can avoid tin overflow in tin plating and greatly improve productive efficiency. This technique is commonly used in the production of terminals and connectors.
Electrolytic Plasma Polishing
Electrolytic plasma polishing can also be called plasma discharge cleaning. It is a technique that utilizes dense cluster arc discharge method and plasma electrochemical surface movement under the influence of high voltage to prepare the surface before physical vapor deposition coating. This procedure can remove burrs on workpiece surfaces and create a very smooth high-gloss finish.
Plasma polishing can be used in magnesium alloys, titanium alloys, stainless steel and tungsten steel, etc. with applications to the manufacture of medical equipment, mobile phone parts, computer products, electronic appliances, mechanical parts and electronic parts, and to automotive, tooling and hardware industries, etc.
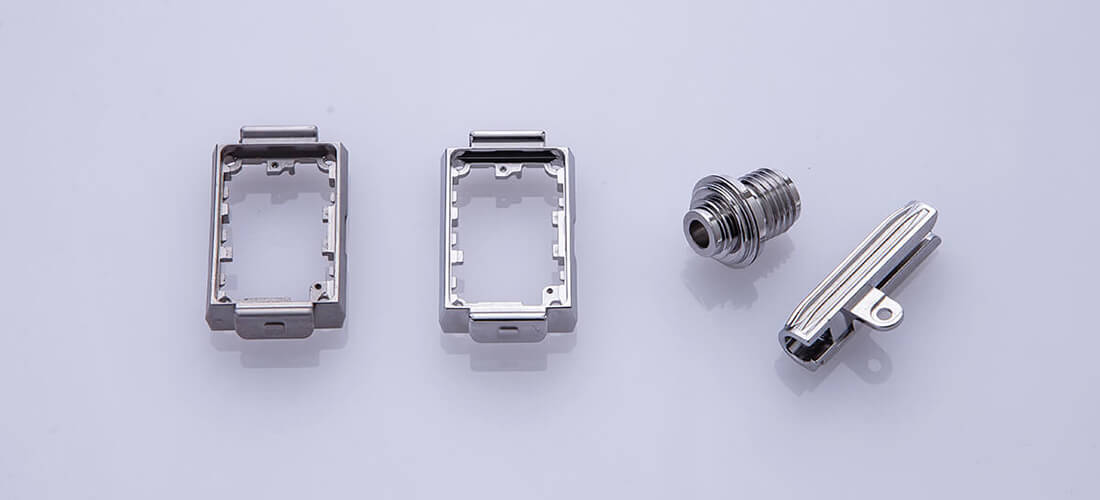
Micro-arc Oxidation (MAO-G)
Micro-arc oxidation (MAO-G), also known as micro-plasma oxidation (MPO), is a method that combines electrolyte and the corresponding electrical energy parameters to generate high temperature and pressure through arc discharge. It is a metal finishing process that utilizes substrate metal oxidation to convert a metallic surface to a ceramic layer.
The micro-arc oxide film is firmly bonded to the substrate with compact structure and highly enhanced toughness. It can seal the micropores on the workpiece surfaces, fuse micro-cracks, remove processing burrs and strengthen surface hardness of the product. The procedure offers significant advantages including improved resistance to wear and tear, corrosion, high temperature and impact, and higher electrical insulation.
The chassis of a laptop or a mobile phone is usually made of plastics coated with aluminum alloy, a case that can be resolved with low temperature micro-arc procedure. In addition, our laboratory can customize raw materials and formulate pigments, and paint surfaces with desired colors to meet specific design requirements.
Micro-arc oxidation is often used in magnesium alloys, aluminum alloys and titanium alloys with applications ranging from the manufacture of automotive parts, computer parts, mechanical components, medical supplies, surgical equipment and instruments, to aerospace and aviation industries, etc.
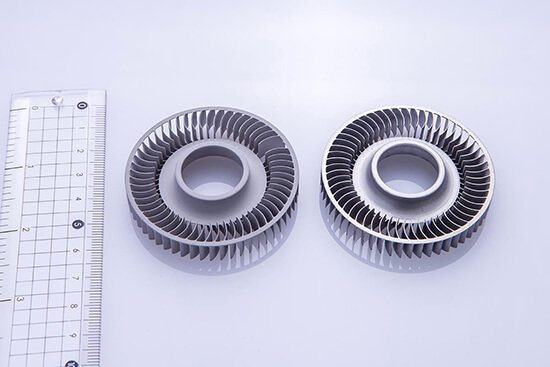
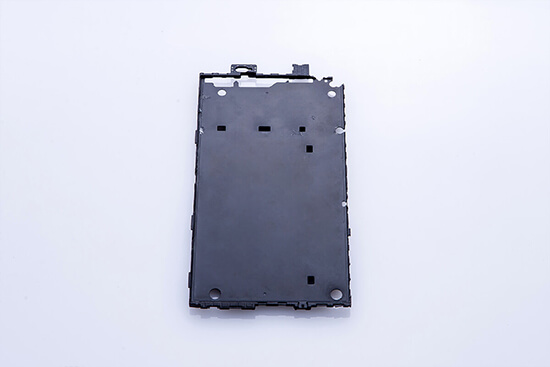